Understanding Precision Injection Mould: A Comprehensive Guide for Metal Fabricators
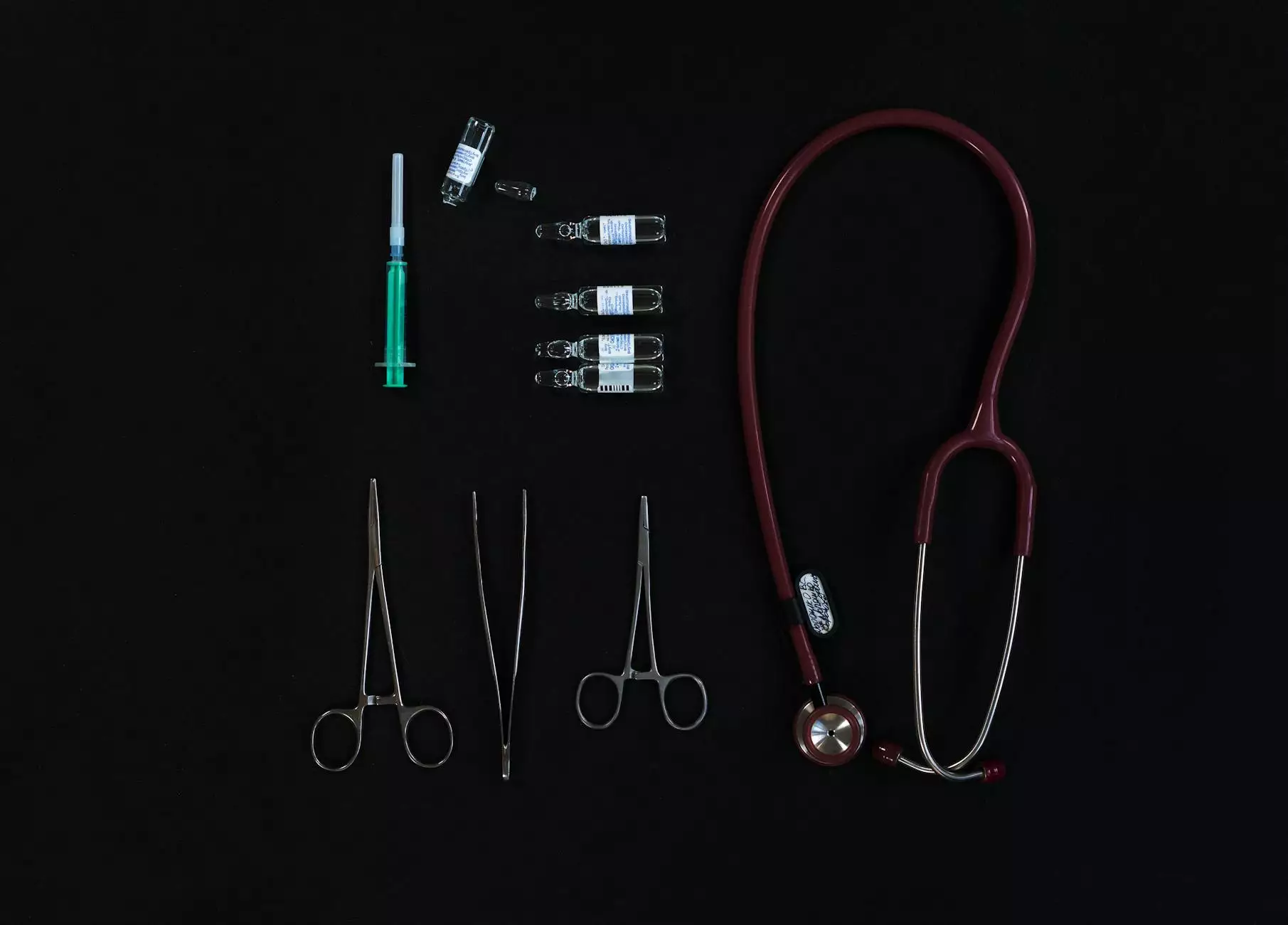
In the ever-evolving landscape of manufacturing, precision injection moulding has emerged as a cornerstone of modern production techniques. This article delves deep into this technology, examining its applications, benefits, and how it can significantly enhance productivity and quality in the metal fabrication industry.
What is Precision Injection Moulding?
Precision injection moulding is a manufacturing process used to create components by injecting molten materials into a mould. This method is particularly favored for its ability to produce intricate and high-precision parts that meet the stringent requirements of various industries.
The Process Explained
- Material Selection: Common materials include thermoplastics, thermosetting polymers, and metals.
- Heating: The selected material is heated until it reaches a molten state.
- Injection: The molten material is injected into a pre-designed mould under high pressure.
- Cooling: The material cools and solidifies to take the shape of the mould.
- Demoulding: The final product is ejected from the mould, ready for further processing or assembly.
Why Choose Precision Injection Moulding?
There are several reasons why precision injection moulding is a preferred choice for manufacturers, especially in the metal fabrication sector:
1. Enhanced Accuracy and Consistency
Precision injection moulding enables manufacturers to achieve extremely tight tolerances, ensuring that each component produced is consistent with the specifications. This level of accuracy is vital in industries such as automotive and aerospace, where safety and performance are paramount.
2. Cost-Effectiveness for High Volumes
Although the initial setup costs may be high due to the need for custom moulds, the cost per unit decreases significantly as production scales up. This makes precision injection moulding an economically viable option for mass production.
3. Complex Geometries
The capability to produce intricate designs that would be challenging or impossible to achieve with traditional manufacturing methods is one of the standout advantages of precision injection moulds. This flexibility allows metal fabricators to innovate and expand their product offerings.
Applications of Precision Injection Moulding
Precision injection moulding finds applications across various sectors:
A. Automotive Industry
From dashboard components to intricate engine parts, the automotive industry relies heavily on precision moulding for producing lightweight and durable parts that enhance vehicle performance and efficiency.
B. Medical Devices
In the medical sector, devices such as syringes, surgical tools, and implantable components are often manufactured using precision injection moulding to ensure patient safety and compliance with strict regulations.
C. Consumer Electronics
The fast-paced world of consumer electronics demands innovative designs and rapid production. Precision moulding enables manufacturers to produce high-quality casings and components that meet consumer expectations for performance and aesthetics.
Benefits of Precision Injection Moulding for Metal Fabricators
For metal fabricators, integrating precision injection moulding into their operations can offer numerous advantages:
1. Reduced Waste
Compared to traditional methods, precision moulding generates less scrap material, contributing to a more sustainable production process.
2. Faster Production Cycle
Once the mould is created, producing parts with precision injection is rapid, allowing for shorter lead times and quicker delivery to customers.
3. Improved Product Quality
The controlled environment of injection moulding minimizes defects, ensuring that each product meets high-quality standards.
4. Versatility
Precision injection moulding can be adapted to produce parts from various materials, allowing for greater flexibility in product design and functionality.
Choosing the Right Partner for Precision Injection Moulding
Selecting the right manufacturer for precision injection moulding is crucial for achieving desired outcomes. Here are key factors to consider:
1. Expertise and Experience
Look for a partner with a proven track record in precision injection moulding. Their experience will ensure they can meet your specific requirements.
2. Technological Capabilities
Ensure they utilize advanced machinery and technologies that enhance production efficiency and output quality.
3. Quality Assurance Procedures
A reputable manufacturer should have stringent quality control processes to ensure that every part meets industry standards.
4. Customer Support and Communication
A strong partnership requires effective communication. Ensure that the manufacturer values collaboration throughout the production process.
Future Trends in Precision Injection Moulding
As technology advances, the field of precision injection moulding is poised for several exciting trends:
A. Automation and Smart Manufacturing
The rise of automation and Industry 4.0 technologies will streamline the moulding process, reducing lead times and enhancing efficiency.
B. Sustainability Efforts
Manufacturers are increasingly focusing on sustainable practices, including the use of recyclable materials and energy-efficient processes.
C. Advanced Materials
Innovations in material science are expanding the range of substances that can be injected, leading to stronger and more versatile parts.
Conclusion
In summary, precision injection moulding represents a vital technology that benefits the metal fabrication industry through its precision, efficiency, and versatility. By understanding the intricacies of this process and its myriad advantages, metal fabricators can leverage it to improve their operations, innovate their product lines, and enhance their competitiveness in the market.
For expert services in precision injection moulding and more, visit deepmould.net to explore our comprehensive offerings tailored for metal fabricators.