The Ultimate Guide to Metal Die Casting: Techniques, Benefits, and Applications
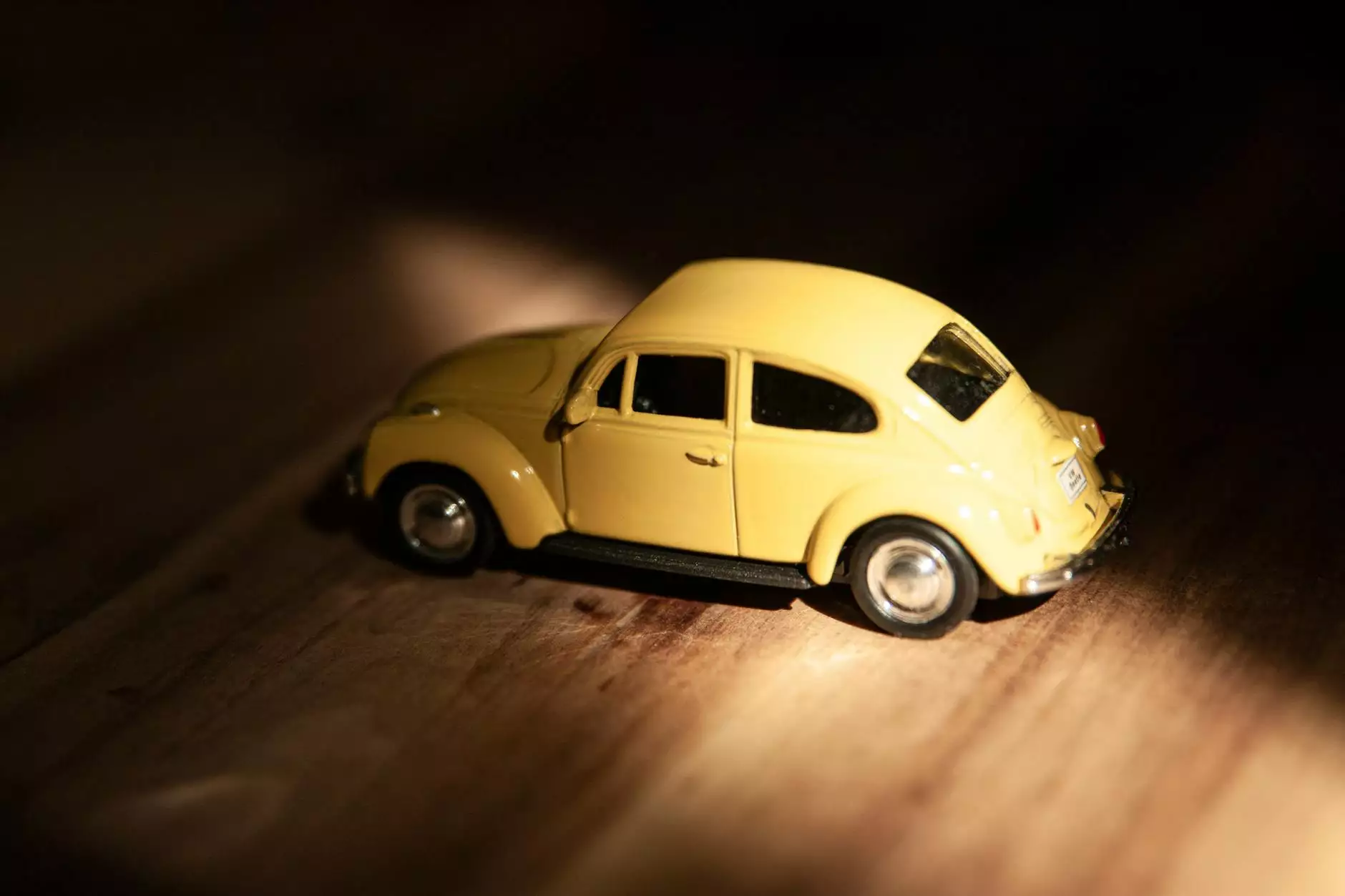
Metal die casting is a manufacturing process that has transformed the landscape of various industries by providing high-quality, precise, and efficient production methods. This article dives deep into the world of metal die casting, exploring its advantages, various techniques, and its applications across multiple sectors. Our goal is to give you a comprehensive overview that can help you understand why metal die casting is a vital process for many businesses and how it can enhance production capabilities.
Understanding the Basics of Metal Die Casting
At its core, metal die casting involves the injection of molten metal into a mold to create intricate and precise shapes. The two primary types of die casting are:
- High-Pressure Die Casting: Uses high pressure to inject molten metal into a mold, resulting in high precision and smooth finishes.
- Low-Pressure Die Casting: Utilizes lower pressure to fill the mold, often used for larger and more complex shapes requiring thicker walls.
This process is widely recognized for its ability to produce consistent and complex geometries that would be difficult or impossible to achieve through traditional machining processes.
The Advantages of Metal Die Casting
Businesses opt for metal die casting due to its numerous advantages, including:
- Precision and Accuracy: The process allows for tolerances as close as ±0.005 inches, providing exceptional dimensional consistency.
- High Production Rates: The efficiency of die casting means parts can be produced quickly, ensuring a rapid turnaround time.
- Material Versatility: A variety of metals, including aluminum, zinc, and magnesium, can be used, catering to different project requirements.
- Improved Surface Finish: Parts produced through die casting have a superior surface finish, reducing the need for additional machining.
- Cost Efficiency: While the initial investment for molds may be high, mass production significantly reduces the cost per unit.
Key Techniques in Metal Die Casting
While the basic process of metal die casting remains consistent, there are several techniques that can be employed to optimize production:
1. Die Design and Construction
The design of the die is crucial to the success of the casting process. A well-designed die will:
- Facilitate efficient metal flow
- Allow for easy ejection of the finished part
- Support cooling and heating processes to prevent defects
2. Mold Filling and Solidification
Understanding the dynamics of how molten metal fills the mold and solidifies is key to reducing defects. Proper control of filling speed and temperature can lead to a higher quality finish.
3. Post-Casting Treatments
After casting, parts may require additional treatments such as:
- Heat Treatment: To improve mechanical properties.
- Surface Treatment: For enhanced corrosion resistance and appearance.
Applications of Metal Die Casting
Metal die casting finds its applications in numerous industries due to its versatility and quality. Some of the most prominent fields include:
1. Automotive Industry
The automotive industry is one of the largest consumers of die-cast components. Parts such as engine blocks, transmission housings, and structural components are routinely produced using metal die casting.
2. Electronics
In the electronics realm, die casting is used to create casings for various devices, providing both protection and aesthetic appeal.
3. Aerospace
In aerospace, precision is paramount. Die casting is utilized for components that require high strength-to-weight ratios and must meet stringent safety standards.
4. Consumer Products
From kitchen appliances to decorative items, the versatility of metal die casting allows for the production of a wide range of consumer products, enhancing durability and appeal.
The Future of Metal Die Casting
The future of metal die casting looks bright, with technology continually evolving. Innovations such as:
- 3D Printing of Molds: This technology allows for rapid prototyping and reduced lead times.
- Automated Systems: Increased automation in die casting processes is enhancing efficiency and precision.
- Advanced Alloys: The development of new metal alloys is expanding the capabilities and applications of die casting.
These advancements are likely to make die casting even more attractive for various industries, cementing its role in modern manufacturing.
Choosing the Right Metal Fabricator for Die Casting
When considering metal die casting for your projects, selecting the right fabricator is crucial. Look for a company that:
- Has extensive experience in die casting
- Offers a range of services from design to post-production
- Uses state-of-the-art equipment
- Provides quality assurance through rigorous testing
At Deep Mould (deepmould.net), we pride ourselves on being leaders in metal die casting. Our knowledge, experience, and commitment to quality make us the perfect partner for your manufacturing needs.
Conclusion
In conclusion, metal die casting stands out as a remarkable manufacturing process that offers numerous benefits across multiple industries. Its ability to produce high-quality, precise, and efficient components makes it indispensable in today's fast-paced market. As technology continues to advance, the potential applications and improvements in this field are endless. Partnering with a reputable fabricator like Deep Mould ensures that businesses tap into the full potential of metal die casting, leading to successful production outcomes.