Understanding the **Hot Alignment of Pumps**: A Comprehensive Guide for Businesses
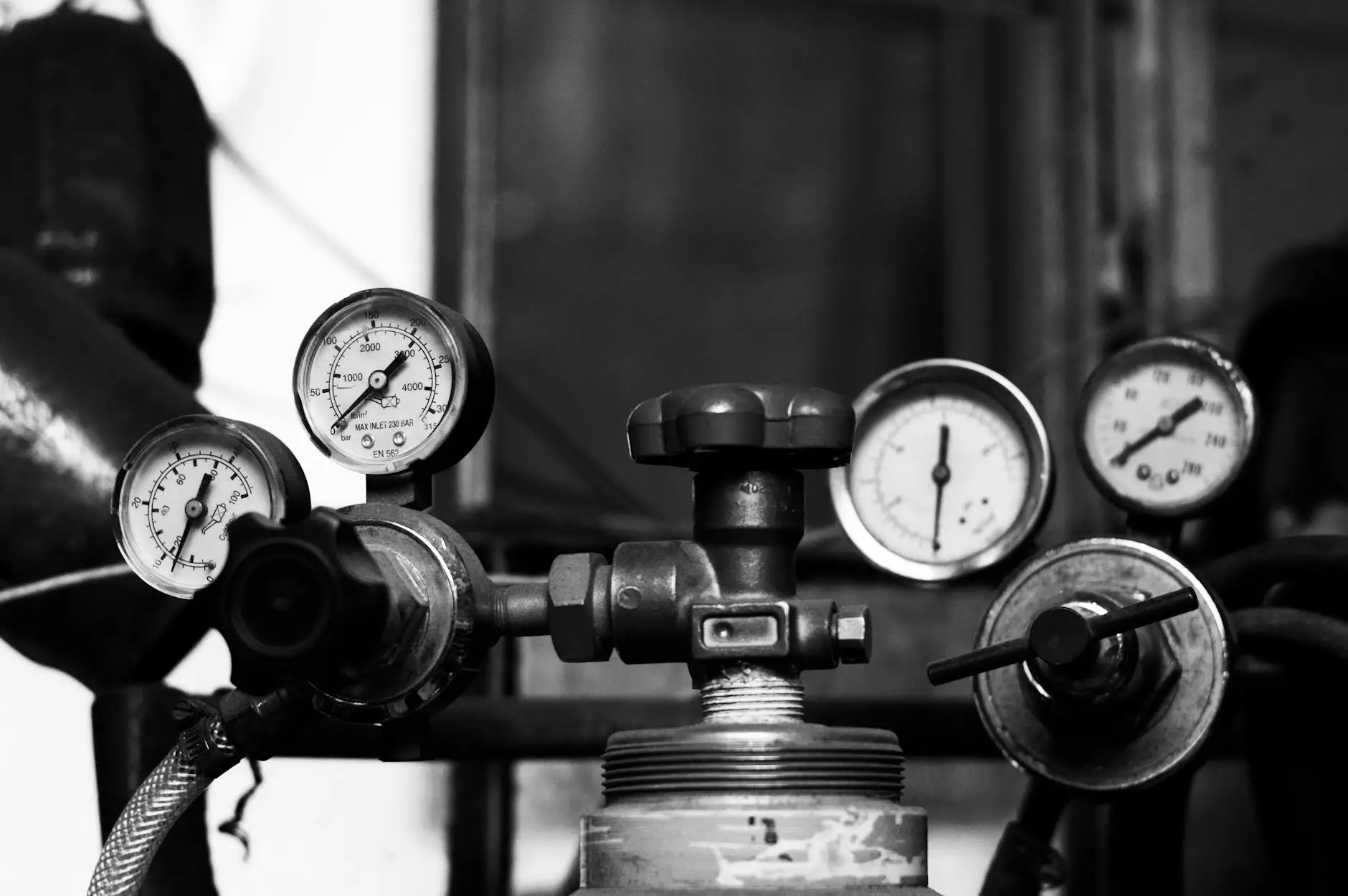
The hot alignment of pumps is a crucial process in maintaining operational efficiency within various industries, particularly in sectors like auto repair, farm equipment repair, and structural engineering. Proper alignment of pumps not only enhances performance but also extends the lifespan of equipment, ultimately leading to significant cost savings. In this article, we will explore the intricacies of hot alignment, its benefits, techniques, and best practices to ensure your business operation remains seamless.
What is Hot Alignment?
Hot alignment refers to the adjustment of pump components while they are operating under normal conditions. This contrasts with cold alignment, where adjustments are made when all components are static and at room temperature. Understanding the differences and implications of these methods is essential for achieving the best results in pump maintenance.
Why is Hot Alignment Important?
The need for hot alignment arises from the fact that machinery expands when it is operating. When pumps and their associated components heat up, the physical changes can lead to misalignment, which may result in various operational issues. Here are some key reasons why implementing hot alignment techniques is critical:
- Increased Reliability: Properly aligned pumps reduce the risk of operational failures, leading to fewer interruptions and downtimes.
- Cost Efficiency: By preventing wear and tear caused by misalignment, businesses can save on repairs and replacement costs in the long run.
- Enhanced Performance: Efficient pump operations maximize productivity and ensure that systems operate at optimal levels.
- Reduced Energy Consumption: Aligned pumps operate more efficiently, leading to lower energy costs, which is beneficial for environmental sustainability as well.
Common Hot Alignment Techniques
Several techniques can be used to achieve effective hot alignment of pumps. The choice of technique often depends on the specific machinery and operational conditions. Here are some widely recognized methods:
1. Laser Alignment
Laser alignment is one of the most advanced techniques available today. This method utilizes laser beams to precisely measure the alignment of pump shafts. It offers high accuracy and can quickly identify misalignment without requiring excessive downtime. Laser alignment systems can also provide real-time feedback, making adjustments easier and more efficient.
2. Dial Indicator Alignment
This traditional method employs mechanical dial indicators to measure shaft alignment. While it may not be as advanced as laser systems, it is still quite effective, especially for certain types of equipment. Technicians manually adjust the pump until readings fall within acceptable limits, ensuring proper alignment.
3. Bump Test
The bump test is a relatively simple technique where the operator applies a bump or jolt to the equipment to observe its response. This method can help identify misalignment, but it is generally less precise compared to laser or dial indicator methods. It is often used as a preliminary check before conducting more detailed alignment procedures.
Best Practices for Hot Alignment of Pumps
To ensure successful hot alignment processes, businesses should adhere to several best practices:
1. Regular Monitoring
Implement a routine monitoring schedule to check alignment regularly. Early detection of misalignment can prevent extensive damage and costly repairs.
2. Use Advanced Tools
Investing in high-quality alignment tools, such as laser alignment systems, can lead to more accurate results. These tools help minimize errors and increase the reliability of readings.
3. Training and Expertise
Ensure that personnel performing hot alignment are well-trained and understand the principles of alignment. Having knowledgeable staff is vital for the successful implementation of alignment procedures.
4. Document Findings and Adjustments
Maintain thorough records of alignment checks, adjustments made, and any observations during the process. This documentation can be invaluable for future reference and helps track performance over time.
5. Understand Manufacturer Guidelines
Each pump and component may have specific alignment requirements. Adhering to the manufacturer's guidelines will ensure compliance and optimal performance.
Benefits of Proper Hot Alignment
Implementing effective hot alignment practices yields numerous benefits that extend beyond operational efficiency. Let’s explore some of these advantages:
- Increased Equipment Life: Proper alignment significantly reduces wear on bearings and seals, prolonging the lifespan of the pump.
- Improved Safety: Aligned pumps operate more smoothly, reducing the risk of accidents caused by vibrations or unexpected failures.
- Higher Production Rates: With less downtime and fewer repairs, production processes can run uninterrupted, increasing overall productivity.
- Less Noise and Vibration: Proper alignment minimizes vibrations, leading to quieter operations and a better working environment.
Conclusion: Elevate Your Operations with Hot Alignment of Pumps
In conclusion, the hot alignment of pumps is an essential practice that can lead to significant improvements in operational reliability, cost efficiency, and safety. By embracing advanced alignment techniques, adhering to best practices, and understanding the benefits, businesses in fields such as auto repair, farm equipment repair, and structural engineering can enhance their operational efficiency and reliability.
For those looking to implement or improve their pump alignment strategies, it's crucial to prioritize ongoing training, investment in modern technology, and regular maintenance scheduling. By doing so, your business will not only save costs but also create an environment conducive to growth and success in today's competitive landscape.
Contact Us for More Information
If you are interested in learning more about the hot alignment of pumps and how it can benefit your business, feel free to reach out to us at michael-smith-engineers.co.uk. Let's optimize your equipment for better performance and reliability!